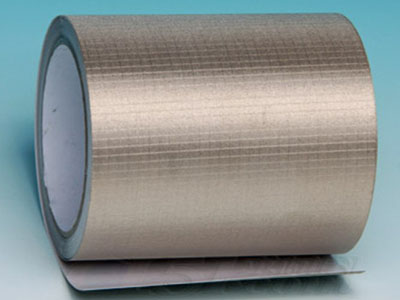
1. Mechanical conditions of rolling mill or other relevant technological conditions required for the qualitative leap of copper strip rolling to copper foil and thickness thinning; This is the essential problem faced by calendering. The fundamental difference between copper foil and copper strip is in its thickness. In China, generally, the difference between copper foil and copper strip is divided by 0.05mm. In the United States, Japan and other countries, it is divided by 0.1mm. In China, the import and export are divided by 0.15mm, mainly considering the current backward situation of domestic copper foil production technology compared with that of foreign countries, while aluminum foil is divided by 0.2mm, Generally speaking, the texture of aluminum and aluminum alloy is softer than that of copper and copper alloy. The aluminum foil rolling theory is that when rolling, the contact arc is equal to the condition that the roll is flattened and the roll gap has been fully pressed. The reduction amount has no absolute relationship with the rolling pressure. The rolling process has been completely completed by controlling the tension and the rolling speed; At present, the rolling process of copper foil is mainly completed by rolling pressure reduction. Therefore, the aluminum foil is generally rolled by four roll irreversible rolling mill, and the aluminum foil with a thickness of 0.0065mm can be produced by double lamination rolling.
2. Surface treatment technology of calendered copper foil in the subsequent process of the production process; It mainly refers to the surface passivation treatment for anti-oxidation corrosion of the copper foil in the later period of use, and the requirement that the calendered copper foil should have the binding ability with the printed circuit board, and have certain chemical resistance, heat resistance, ion migration resistance, etc. With the continuous development of electronic products in the direction of miniaturization and multi-function, the printed board is promoted to develop in the direction of multi-layer, high integration and high density. Therefore, the thin copper foil used in the fine circuit is required to have higher peel strength, and can effectively reduce or avoid the "side corrosion" phenomenon when etching the circuit. In the high-frequency circuit, the copper foil is required to have better ion migration resistance, To prevent the short circuit or open circuit of the line caused by the decrease of the insulation performance of the resin substrate due to ion migration, and the heat resistance temperature of the copper foil is much higher than the original. These properties of the copper foil are closely related to the surface treatment process adopted by the copper foil. The surface treatment technology of copper foil has also become the research hotspot of copper foil manufacturing enterprises in the world. Foreign countries began to carry out in-depth and extensive research on the surface treatment technology of copper foil very early, and developed a variety of surface treatment technologies. However, the domestic research on the surface treatment of copper foil is less and started late.
3. Precise control technology of slab organization during horizontal continuous casting, rolling and heat treatment; At this point, calendered copper foil is obviously different from electrolytic copper foil. Generally, electrolytic copper foil (excluding low profile copper foil) presents the characteristics of columnar structure and developed structure in the thickness direction. During the bending, the gradual propagation of cracks at the particle interface of the columnar structure will cause the structural damage of the copper foil at a relatively early stage when the copper foil moves in the bending and bending. Calendered copper foil is a foil formed by rolling, so the structure structure is thin. After heat treatment, the recrystallized structure changes into equal square. Due to the isotropy of the structure, cracks in the particle interface do not propagate, and thus the flexural resistance is particularly high.
4. The protection of the copper foil surface in the production process; That is, anti-oxidation and corrosion technology in the process of processing and production, surface degreasing and cleaning, pickling, preparation of rolling oil and emulsion in the process of rolling, and protective protection in the process of heat treatment. This is mainly due to the increase of the surface area of the copper foil due to the requirements of its thickness relative to its length and width, which makes it more in contact with the outside world until after the passivation process. At the same time, the important technical parameters of the copper foil in the electronic information technology, surface roughness and subsequent coarsening of the plating layer, also make the surface particularly important. In addition, it is particularly important for the thin thickness of the copper foil under the same oxidation and corrosion depth. In case of improper treatment or process problems, the overall size of the copper foil may be too small, the local size deviation of the copper foil with large thickness, perforation or tearing, and the corrosion pit and crack in the interior may also have a great impact on the transmission of electronic current.